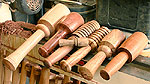 |
Carvers mallets are easy and good practice projects.
Click image to enlarge |
Turning a Carvers Mallet
Letting the wood help
Text & Photos by Tom Hintz
The one-piece carvers mallet is a great project for new woodturners because in its simple forms it is easy to turn but provides good practice with basic turning tools and skills. Start out with simple shapes to build confidence and skills before adding more difficult design elements to increase the challenge at your own pace.
As your skills increase, the basic mallet can morph into nutcrackers, tenderizing hammers or even pestles for mortar and pestle sets. Once the basic procedures are mastered, your creativity is the only limitation when creating gifts, or just having fun on a rainy afternoon.
The mallet in the accompanying photos is admittedly larger than might be considered normal, but I'm not normal and it was fun to turn. It also made a good subject for the photos that illustrate this story. It will remain on-hand in my shop so I never have to wish I had a bigger mallet.
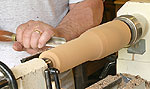 |
After rounding the a basic cylinder, begin generally defining the shape.
Click image to enlarge |
Rough the Blank
Mount the blank securely between centers, set the lathe on a low speed and turn it down to a basic cylinder. I have learned to stop as soon as the blank rounds out to look at the wood. Sometimes defects or grain patterns revealed during rounding a blank makes one end better suited for the mallet head and the other for the handle. The blank used for this story was a glue-up that had a shallow gap along part of the seam that was easily turned away, but made that end most appropriate for the handle.
I like to turn the blank down with the roughing gouge, reducing the handle end a bit more to begin defining the shape very generally. By this point, I have a good idea of the target diameter for the handle and can remove a considerable amount of material from that area with the roughing gouge.
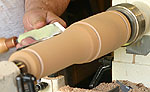 |
Mark the different parts with grooves or pencil lines.
Click image to enlarge |
Mark-Off Segments
With the blank roughly shaped, you can mark where the various features of the mallet are going to begin and end. I used a large skew chisel to make V-grooves defining the head and the handle areas.
I wanted a bead at the top of the handle so after reducing the handle portion close to the diameter of the bead, the largest feature on this part of the mallet, another V-groove was cut defining its width, which also finalizes the length of the handle grip. If there is a bead at the bottom end of the handle, cuts grooves to define that as well.
Shape the Head
Using the large skew chisel, I shaped the curved face of the mallet head. I also began shaping the ends of the mallet head by cutting a gentle angle with the skew.
The upper half of the bead was also trimmed to better define the V-groove that separates it from the mallet head. Because of this mallet is so large, and will be used to hit things in the shop, I left 1 ½" material at the narrowest spot between the bead and head.
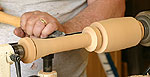 |
With most of the excess material removed the individual shapes can be roughed in.
Click image to enlarge |
The lower side of the bead was also rough-shaped to begin forming the junction between it and the handle surface.
Shape the Handle
I used the roughing gouge and then the large skew to take the handle down to near finish diameter. I like to work the basic shape of the handle in with the roughing gouge to remove material quickly and then switch to the large skew to refine the handle shape and smooth the surface. As the handle approached finish diameter the bead is also refined to keep the junction between it and the handle clean.
Refine Shapes
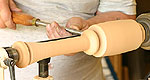 |
Keeping the bevel rubbing through the final cuts drastically reduces the amount of sanding that will be needed before finishing.
Click image to enlarge |
Using skews and spindle gouges, finish cuts were taken on the entire mallet. At this point, all of the shapes are given final cuts to smooth their surfaces and reduce the amount of sanding necessary.
To finish the handle, I made two small v-grooves near the handle butt for decoration.
Trim Ends
With all the chisel work complete I used a parting tool to reduce the material supporting the mallet to about 3/8"-diameter. The wood looked and sounded solid at both ends so this should be enough material to hold a mallet of this size during finishing.
Be careful with this part of the process. If the wood looks at all suspect, leave more material at the ends and saw the piece off after finishing. It is better to spend some time sanding the ends after cutting them off than to have the piece fly out of the lathe at finishing RPM and knock you out.
Sand & Finish
Because of the finish left by the skew and spindle tools, I was able to start sanding with 220-grit and quickly work down to a 600-grit finish.
Because the mallet would be used in the shop, I chose not to oil it. After blowing off the dust with compressed air and going over it with a tack rag I ran the lathe up to the highest speed I was comfortable with and applied Hut PPP natural gloss wax, burnishing it in with a clean rag. One more light coat of the Hut PPP followed by a final polishing and the mallet was ready to come off the lathe.
Parting Off and Clean Up
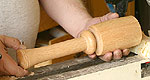 |
The finished mallet with just a simple wax finish. It took about 15 minutes to turn.
Click image to enlarge |
With the lathe on the slowest speed, I used the point of the ¾" skew to reduce the remaining wood at the butt end and then to part off the mallet at the headstock. I like making the actual separation cut at the headstock so the workpiece stops spinning, making it easier to catch and shut the lathe off.
If parting the finished piece off a spinning lathe is at all threatening, remove the piece and saw the waste off the ends.
A sharp knife cleaned up the remaining strands of wood. A little sanding prepared the ends for touch up waxing followed by hand buffing and the mallet was done.
The process of roughing the blank in stages to pick where features can best be located sounds more time-consuming than it really is. Once you get used to it, and gain a bit of confidence with the roughing tools, blanks can be brought to rough shape very quickly. Being able to actually see the grain and defects as they are revealed allows for making better decisions on what feature should go where, regardless of the project. These options are not always available, but when they are, this process allows taking full advantage of what the wood offers.
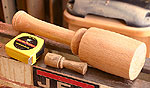 |
Big or small, carvers mallets are fun to make and improve your tool control in the process.
Click image to enlarge |
Carver mallets are fun to make and a great way practice a wide range of basic turning skills many chisel types. Mallets can be turned from virtually any wood though hardwood is the best choice for those meant to be used.
If you are new to turning, start with simple designs and then add features one at a time as your confidence and skills grow. You will be surprised at how fast the complexity of mallets and your comfort-level making them increases. |